Battery separators are the unsung heroes within the realm of battery technology. In this comprehensive guide, we will explore the fascinating world of battery separators, shedding light on their definition, functions, types, and the intricate process involved in their manufacturing. Join us on this enlightening journey as we uncover the crucial role of battery separators in energy storage.
Part 1. What is a battery separator?
At the heart of every battery lies a critical component, the battery separator. This thin and porous material acts as a physical barrier between the positive and negative electrodes of the battery, preventing direct contact between them. By maintaining this separation, the battery separator ensures the smooth flow of electricity and prevents potential short circuits.
Part 2. Functions of battery separators
1. Electrolyte Management
Battery separators play a vital role in managing the movement of electrolytes within the battery. Electrolytes are conductive substances that enable the flow of ions between the positive and negative electrodes, facilitating the electrochemical reactions that generate electricity. The separator helps ensure a uniform distribution of electrolytes, optimizing ion transport and enhancing the overall battery performance.
2. Ion Transport
One of the primary functions of a battery separator is to facilitate the transport of ions between the electrodes. During the charging and discharging processes, ions, such as lithium ions in lithium-ion batteries, must migrate through the separator to maintain the electrochemical balance. The porous structure of the separator allows controlled ion flow while preventing electrode contact, which could lead to short circuits.
3. Electrical Insulation
Battery separators act as effective electrical insulators between the positive and negative electrodes. By preventing direct contact between the electrodes, they eliminate the risk of short circuits that may cause battery failure or pose safety hazards. The separator’s insulating properties ensure the electrical current flows through the intended path, optimizing battery performance and longevity.
4. Mechanical Support
In addition to their electrical functions, battery separators provide mechanical support to the electrodes. They help maintain proper spacing between the electrodes, preventing deformation or physical damage during battery operation or external stress. The structural integrity of the separator is crucial for the overall stability and durability of the battery.
Part 3. Types of battery separators
1. Polymeric Separators
Polymeric separators are widely used in various battery technologies, particularly lithium-ion batteries. These separators are typically made from polyethylene (PE) or polypropylene (PP). Polymeric separators offer excellent dielectric properties, thermal stability, and mechanical strength. They can be manufactured with different pore sizes and thicknesses to meet the specific requirements of different battery applications.
2. Ceramic Separators
Ceramic separators are known for their exceptional thermal stability and mechanical strength. They find battery applications that require enhanced safety features or operate at high temperatures. Ceramic separators are made from aluminum oxide (Al2O3) or lithium aluminum titanium phosphate (LATP). These materials exhibit excellent thermal and chemical stability, low electrical conductivity, and resistance to mechanical stress.
3. Glass Fiber Separators
Glass fiber separators are created by weaving thin glass fibers together to form a porous structure. These separators offer good mechanical strength, chemical resistance, and dimensional stability. They are commonly used in lead-acid batteries and applications that require high absorbency and acid resistance.
4. Nonwoven Separators
Nonwoven separators are manufactured by entangling synthetic fibers to create a porous structure. These separators are lightweight, flexible, and exhibit good resistance to acid and electrolyte degradation. Nonwoven separators are commonly employed in batteries such as nickel-metal hydride (NiMH) batteries and alkaline batteries.
Part 4. Battery separator manufacturing process
The manufacturing process of battery separators can be broadly categorized into two methods: wet and dry.
Wet Process Manufacturing
The wet process is widely used for manufacturing battery separators, especially polymeric materials.
- Polymer Solution Preparation: The first step in the wet process involves preparing a polymer solution. The selected polymer, such as polyethylene (PE) or polypropylene (PP), is dissolved in a suitable solvent to create a homogeneous solution. This solution will serve as the precursor for the separator material.
- Coating or Casting: The polymer solution is then coated or cast onto a moving substrate, such as a conveyor belt or rotating drum. The coating thickness is carefully controlled to achieve the desired separator thickness.
- Solvent Removal: After the coating process, the separator goes through a drying stage to remove the solvent from the polymer. This can be done through various methods, such as evaporation or hot air drying. The drying process ensures the solidification of the polymer and the formation of a porous structure.
- Calendering: In some cases, the separator may undergo a calendering process. Calendering involves passing the separator material through rollers to enhance its thickness uniformity and smoothness further. This step helps improve the mechanical strength and overall quality of the separator.
- Pore Formation: The separator may undergo a pore formation process to create the necessary porous structure. This can be achieved through stretching, heat treatment, or controlled mechanical deformation. The pore formation step is crucial for optimizing the separator’s electrolyte management and ion transport properties.
- Finishing and Quality Control: The manufactured separators undergo various finishing processes, such as trimming the edges and ensuring uniformity in thickness and pore size distribution.
Advantages:
- Produces uniform and high-quality separators.
- Allows precise control over thickness and porosity.
- Incorporates additives for enhanced functionality.
Limitations:
- Time-consuming and energy-intensive drying process.
- Solvent use in coatings may pose environmental concerns.
Dry Process Manufacturing
The dry process is commonly employed for manufacturing ceramic-based battery separators.
- Powder Mixing: The first step in the dry process is to mix the ceramic powders with binders and additives. The composition of the mixture is carefully controlled to achieve the desired properties in the final separator.
- Sheet Formation: The mixed powder is then compacted and formed into sheets using roll pressing or tape casting methods. The sheets are typically thin and flexible, ready for further processing.
- Drying and Binder Removal: The formed sheets are subjected to a drying process. This step removes the binders and any remaining solvents, leaving a solid ceramic structure behind. The drying temperature and duration are controlled to ensure proper binder removal without causing damage to the separator.
- Sintering: The dried ceramic sheets undergo a sintering process and are heated to high temperatures in a controlled atmosphere. Sintering causes the ceramic particles to bond, resulting in a dense and mechanically robust separator structure.
- Pore Formation: Similar to the wet process, the dry process also includes a pore formation step. Various techniques, such as controlled thermal treatment or chemical etching, are employed to create the desired porous structure in the ceramic separator.
- Finishing and Quality Control: The finished ceramic separators undergo final finishing processes, including trimming, thickness measurement, and quality control checks.
Benefits:
- Efficient and scalable production.
- Consistent properties across batches.
- Flexibility to tailor properties for specific requirements.
Limitations:
- Requires specialized equipment for extrusion and stretching.
- Its ability to incorporate additives compared to wet process coatings is limited.
Part 5. Conclusion
By exploring the definition, functions, types, and manufacturing process of battery separators, we hope to have provided you with valuable insights into this crucial aspect of battery technology. As you delve further into the fascinating world of batteries, remember the significant role of battery separators in powering our modern lives.
Related Tags:
More Articles
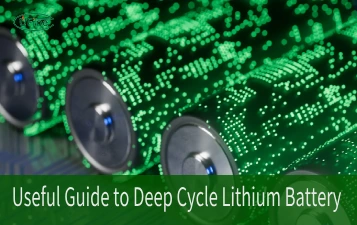
Overview of Deep Cycle Lithium Battery
In this article, we explore the life, voltage, capacity, and charging considerations of deep cycle lithium batteries.
How Long do Lithium Batteries Last?
How long do lithium batteries last? we will explore the factors that influence the lifespan of lithium batteries and provide insights into their longevity.
How to Choose the Best LiFePO4 Battery?
Choose LiFePO4 batteries for superior performance, safety, and versatility in EVs, UPS, and backup power. This guide helps you make informed decisions.
Get 12v Lithium Car Battery As a Power Source for the Ride
Make the right choice for your vehicle's battery needs by installing a 12 volt lithium car battery. You will enjoy maintenance-free longevity with this change.
Everything About A Small Lithium Ion Battery
Discover the features, uses & future potential of a small lithium ion battery. A compact and tiny powerhouse ideal for smartphones, wearables, drones & more.